液態硅膠(LSR)技術近年來通過材料科學、工藝創新和智能化制造的深度融合,實現了從模具設計到終端應用的全鏈條升級。尤其在精密電子、醫療健康、新能源等領域的突破性應用,標志著LSR技術從“輔助材料”向“功能化核心組件”的跨越。以下是技術革新的關鍵路徑和未來潛力分析:
一、模具制造:精度與效率的顛覆性突破
智能模具設計
AI驅動的模流仿真:通過機器學習算法優化模具流道設計,預測材料填充過程的氣泡、縮痕等缺陷,良率提升30%以上(如Moldflow與LSR專用軟件的深度結合)。
納米級表面處理:采用類金剛石涂層(DLC)或微弧氧化技術,模具壽命延長5倍以上,同時實現LSR制品表面無痕脫模。
隨形冷卻水路:3D打印技術制造的異形冷卻通道,使模具溫度均勻性誤差<±1℃,顯著縮短成型周期。
柔性制造革命
模塊化模具系統:針對多品種、小批量需求(如醫療器械),通過快速換模技術實現“一機多模”,切換時間縮短至10分鐘內。
增材制造模具:金屬3D打印的隨形鑲件,解決傳統加工中無法實現的微流道(<0.2mm)和仿生結構。
二、材料創新:從性能增強到功能化
高性能配方突破
耐極端環境型LSR:耐溫范圍擴展至-60℃~300℃(如瓦克化學的SilGel®系列),耐受強酸、強堿和輻射環境。
導電/導熱改性:添加氮化硼、碳納米管等填料,導熱率提升至5 W/m·K以上(如邁圖的TC-5005),滿足5G基站和電動汽車功率模塊散熱需求。
生物相容性與安全性
醫療級LSR:通過ISO 10993認證,用于長期植入器械(如心臟起搏器密封件),并開發抗菌型LSR(摻入銀離子或光觸媒材料)。
食品接觸安全:符合FDA 21 CFR 177.2600標準,用于嬰幼兒用品和智能廚電密封件。
三、成型工藝:從規模化到超精密
多物理場耦合注塑技術
電磁輔助成型:通過磁場控制LSR分子鏈取向,提升特定方向力學性能(如彈性模量定向增強50%)。
真空注塑與壓力反饋:實時調節模腔壓力,消除微米級氣孔,用于光學級LSR透鏡(透光率>92%,霧度<1%)。
微納尺度制造
微針陣列注塑:制造直徑<50μm的醫療微針(如血糖監測貼片),突破傳統PDMS的力學強度局限。
LSR與電子元件共集成:在注塑過程中直接嵌入柔性電路(如MEMS傳感器),實現“結構-功能”一體化(案例:特斯拉電池組密封與應力監測集成模塊)。
四、電子灌封:高可靠性的核心保障
高頻高速場景適配
超低介電材料:介電常數(Dk)<2.8,損耗因子(Df)<0.001,滿足毫米波雷達和6G通信設備需求(如信越的KE-1955系列)。
電磁屏蔽LSR:添加磁性粒子(如羰基鐵粉),實現30dB以上的寬頻段屏蔽效能。
新能源領域創新
電池包灌封:耐電解液腐蝕LSR(如陶氏DOWSIL? CC-2588),用于4680電池模組密封,-40℃下仍保持彈性。
氫燃料電池雙極板密封:耐氫脆、耐高壓(>3MPa)的LSR方案替代傳統橡膠,壽命提升至2萬小時以上。
五、未來趨勢:綠色化與智能化
循環經濟驅動
化學回收技術:開發LSR閉環回收工藝(如熱裂解再生硅氧烷單體),減少工業廢料。
生物基LSR:以蓖麻油等可再生資源替代石油基原料(科思創已推出實驗性產品)。
數字孿生與智能監控
IOT賦能產線:通過嵌入式傳感器實時監測LSR硫化程度和應力分布,動態調整工藝參數(如恩格爾的iQ系列控制系統)。
區塊鏈溯源:從原材料到終端產品的全生命周期數據上鏈,滿足醫療和汽車行業的合規性要求。
結語
液態硅膠技術的革新已突破單一材料屬性優化的范疇,轉向與終端應用場景的深度耦合。未來,隨著AI、量子計算等技術的滲透,LSR將向“自適應材料”(如溫敏/形變響應型)和“能源-信息載體”方向演進,成為下一代智能硬件的基石材料之一。企業需重點關注 “精密化+功能化+可持續” 三位一體的技術布局,以搶占高端制造制高點。
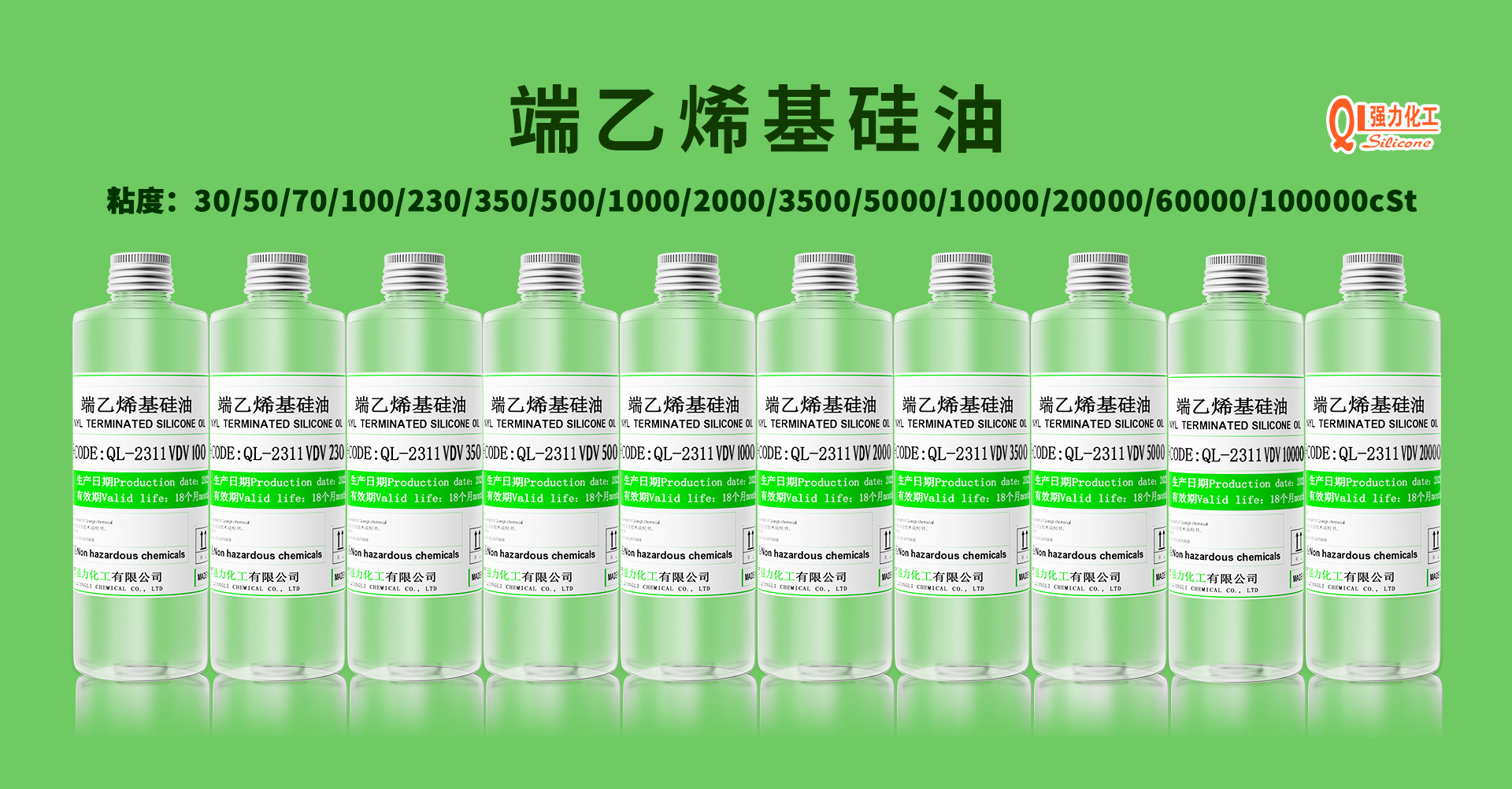